Supervisory Control Synthesis for Energy Efficient BIS Chiller Plants
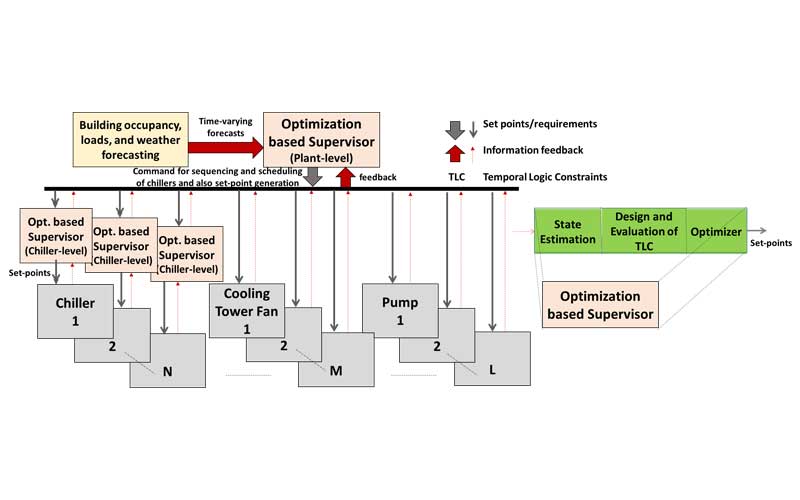
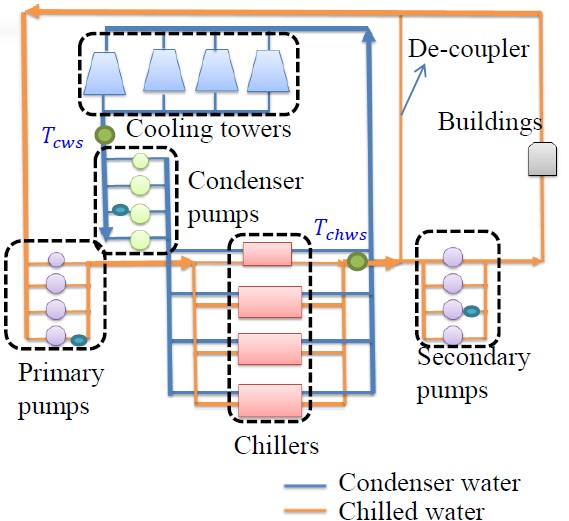
Principal Investigator
Graduate Fellows
Pavan Thota, James Wilson, Khushboo Mittal,
Danxu Zhang, Brian Baillie, Hebatullah Ibrahim
Co-Principal Investigators
Project Duration
2015-2017
Building HVAC systems consist of chillers, cooling towers, air handling units (AHU), variable air volume systems (VAVs), fan coil units (FCU), makeup air units (MAU), and their associated components (e.g., compressor, condenser, and evaporator in a chiller). These systems and their
components have various operational and safety constraints and are interconnected via different electrical, mechanical, hydraulic or pneumatic connections along with various control loops; thus making the overall system complex. This complexity along with uncertain operating conditions such as time-varying cooling loads, dynamic weather patterns, and growth of faults makes the energy optimization of chiller plants by near-optimal control a challenging problem. In this regard, the proposed research aims to design supervisory control architecture for energy efficient and resilient chiller plants in accordance to the needs of the UTC.diagram
The key novelty of the proposed approach is a scalable optimization-based supervisory control scheme for energy savings and resilience at the chiller as well as chiller plant level. The supervisory controller will generate near-optimal set-points of different performance variables in the chiller and chiller plant for efficiency maximization under various operational, safety, and computational cost constraints. The supervisor will also target resilient operation of chiller plant in the presence of faults in order to prevent further degradation of the faulty component while meeting the desired performance. The supervisor will be designed to deliver robustness against parametric variability, operational stability, minimum energy consumption, resilience, and minimization of the transient behavior between different set-points and will adapt to predicted cooling load patterns based on history and forecasts of weather, occupancy, etc.
Relevant Publications
Peer Reviewed Papers
D. Zhang, P. B. Luh, J. Fan and S. Gupta (2017). “Chiller Plant Operation Optimization with Minimum Up/Down Time Constraints. “ IEEE Robotics and Automation Letters, vol. 3, no. 1, pp. 9-15.
D. Zhang, P. B. Luh, J. Fan and S. Gupta (2017), “Chiller Plant Operation Optimization: Energy-Efficient Primary-Only and Primary-Secondary Systems.“ IEEE Transactions on Automation Science and Engineering, published online (DOI: 10.1109/TASE.2017.2751605).
K. Mittal, J. P. Wilson, B. Baillie, S. Gupta., G. M. Bollas, & P. B. Luh (2017). “Supervisory Control for Resilient Chiller Plants Under Condenser Fouling.” IEEE Access, vol. 5, pp. 14028-14046.
B. Baillie, G. M. Bollas (2017). "Development, validation, and assessment of a high fidelity chilled water plant model." Applied Thermal Engineering, vol. 111, pp. 477-488.
Conferences
P. K. Thota, A. P. Dani, P. B. Luh and S. Gupta, "Cooling load forecasting for chiller plants using similar day based wavelet neural networks," Complex Systems Engineering (ICCSE), 2015. International Conference on, Storrs, CT, 2015.
D. Zhang, P. B. Luh, J. Fan and S. Gupta, "A decomposition and coordination-based method for chiller plant optimization," Complex Systems Engineering (ICCSE), 2015 International Conference on, Storrs, CT, 2015.
B. Baillie, G. M. Bollas, "Development, validation, and assessment of high-fidelity chilled water plant model," in North America Modelica Users’ Group Meeting, 2015.
Presentation
D. Zhang, P. B. Luh, J. Fan and S. Gupta, “Chiller Plant Operation Optimization with Minimum Up/Down Time Constraints,” IEEE Conference on Automation Science and Engineering, Xian, China, August 2017.